Products
Dim Sort Control
Dim Sort Control – A system solution to determine the current dimension of your products and is developed in Siemens PLC. This product can be installed on green sorters or dry sorters and the system measures and sorts the correct thickness and width of the sawn product. The system can be supplemented with length measurement and annual ring detection at the end of the product.
Dim Sort Control – Provides accurate fact-finding for the thickness and width measurement of each individual product. This is done with the help of several laser photocells.
HMI – The operator interface is user-friendly. Viewing takes place in a Touch Panel and there is also access for the system’s various parameters and function of calibration.
System building – Dim Sort Control consists of a device cabinet, laser photocells, encoders, sensor wiring and operator panel.
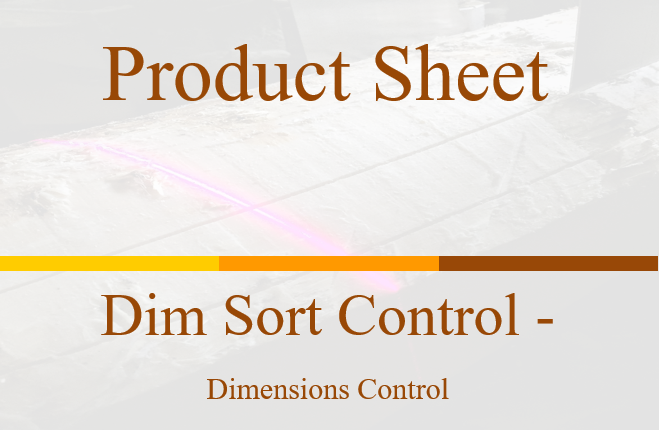
Log Control Tuner
Log Control Tuner – A system solution to optimize your log gap. The System is developed in Siemens PLC. This product can be installed where changes take place between single-piece feed and to the next conveyor. For example, on your Log sorting line, when the logs are paced from the step feeder and down to the measuring conveyor. Another example is at the Saw intake when the logs are paced from the step feeder and down to the receiving conveyor.
Log Control Tuner – Ensures a smooth and constant log gap. The software calculates the current log gap and the system enables catch-up execution function if enabled. The conveyors receive a signal and then accelerate the gaps to the selected value.
HMI – The operator interface is user-friendly. Viewing takes place in a Touch Panel and there is also access for the system’s various parameters. System building–Log Gap Control consists of a PLC, enclosure with laser sensor, photocells and an encoder.
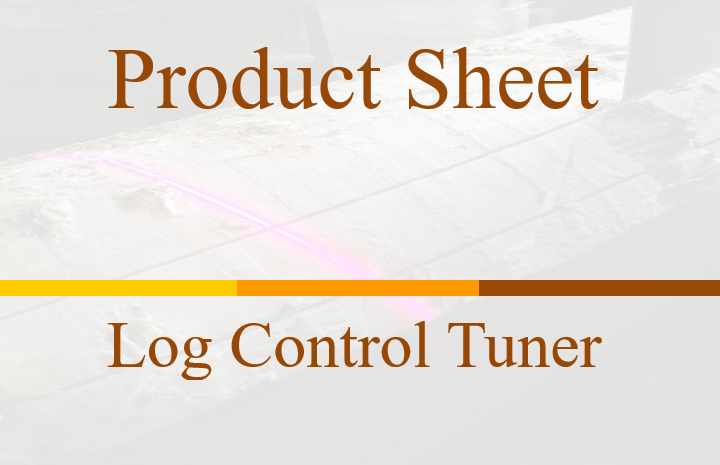
PLC - NMR 2000
All PLC components in NMR 2000 are made by Siemens and we continuously update ourselves with the latest technology to future-proof, both hardware and software. PLC is the S7-1500 series and with choice Failsafe if we also handle machine control together with the safety system. In our system building, our key words are friendly to use and flexibility. We try to use Operator Screens with Touch function at the operator locations as much as possible.
HMI – The operator display is well thought out and well-sized, so that buttons and access to underlying menus are adapted to the Touch function.
Computers, PLC, SQL database hardware, etc. are built into a ventilated main cabinet. This is to ensure a good environment and extend the technical life of the electronics part.
From the PLC cabinet we communicate out to the plant’s I/O nodes, workstations and its equipment via communication bus.
All applications are written in the TIA portal. Programblocks that may be applicable when troubleshooting the customer’s own staff, are written in LAD, other programs in SCL and STL and all well commented. Some application blocks are protected by “know-how-protection” and will not be accessible to the customer.
We perform machine controls, sorting and safety programs for the sawmills’ various processes:
- Log sorters
- Log intakes
- Sawlines
- Green & Dry sorters
- Planer lines
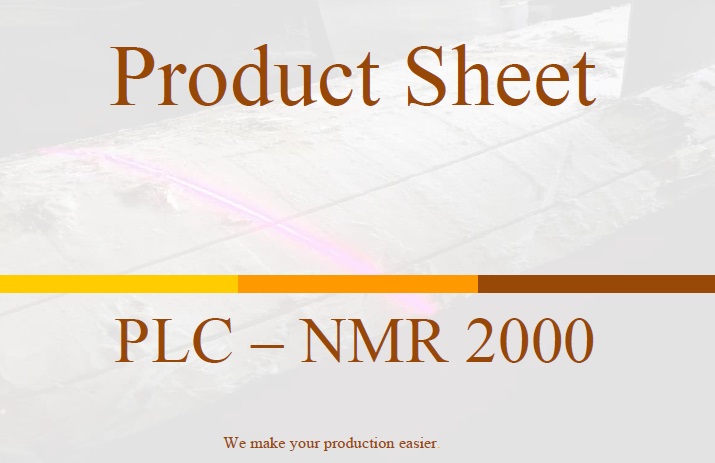
Control Position One
Control Position One – A system solution for servo electronics developed in Siemens PLC. The system is compatible with most of the existing servo valves and sensors handled in the wood industry. Communication between the parent control system of the plant and the control cabinet for Control Position One takes place via the current bus that actual sawmill use. The system solution is adapted to the current facility and nodes mounted at the machine groups communicate with the main unit’s control cabinet.
HMI – The operator interface is user-friendly. Viewing takes place in a Touch Panel and there is also access for the system’s various parameters. As an option, it is also possible to get viewing via PC and computer screen. Sensor Control Position One can handle signal management with analog and digital sensors, SSI and Tempo sonic.
Valves – Control Position One can handle signal handling against Moog and Vickers valves as well as Proportional valves.
Fieldbus – Control Position One handles communication interfaces with the most common fieldbuses, such as Profibus, Ethercat, Modbus
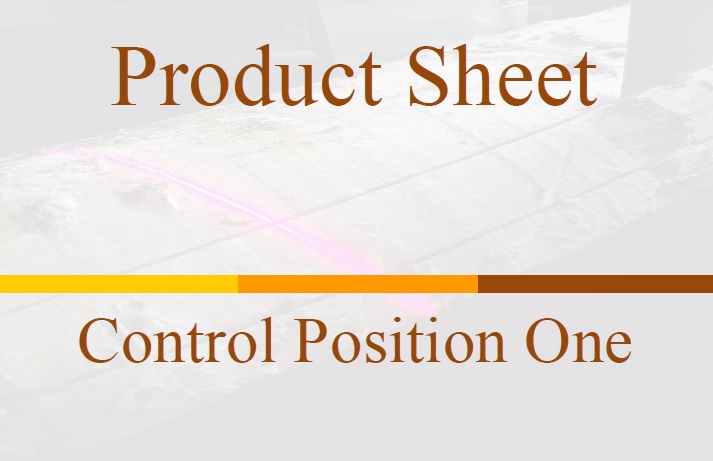
Vision Control - EDGER
Vision Control – EDGER – Is a control system for non-contact measuring of thickness and width measurement at the products processed in an Edging line.
Vision Control – EDGER also measures and controls any “Wedge” i.e. deviations from the intended width measurement. If this discovery is made, an alarm is sent to the operator. Vane, defects and placement according to the length of the edged product are presented in the operator display.
HMI – The operator interface is user-friendly and presented on a computer screen. Average and Standard deviation are presented for each piece and if you want to see how the piece has been sawn from top to but end, there is also a menu selection of that.
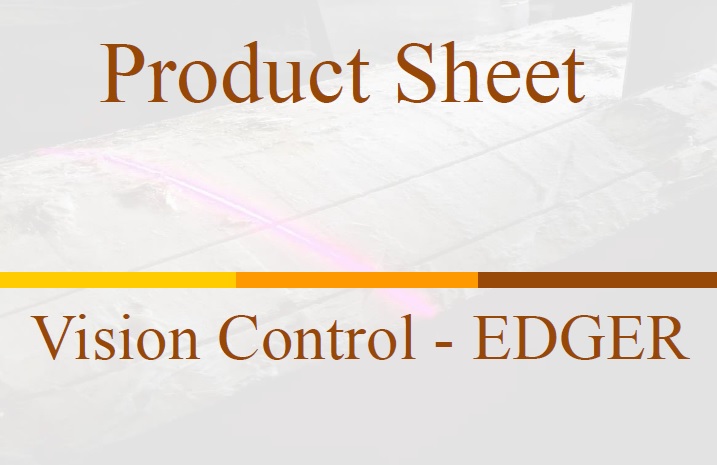
Vision Control - PLANER
Vision Control – PLANER – Is a control system for non-contact thickness and width measurements of the products processed in a planer line.
Vision Control – PLANER – Also measures and controls any “Wedge and deviations” i.e. width and thickness deviations in relation to the intended. If this discovery is made, an alarm is sent to the operator. Vane, defects and the longitudinal position of the planed product are presented in the operator display.
HMI – The operator interface is user-friendly and presented on a monitor. Average and Standard deviation are presented for each piece and if you want to see how the piece has been processed from top to but end, there is also a menu selection of that.
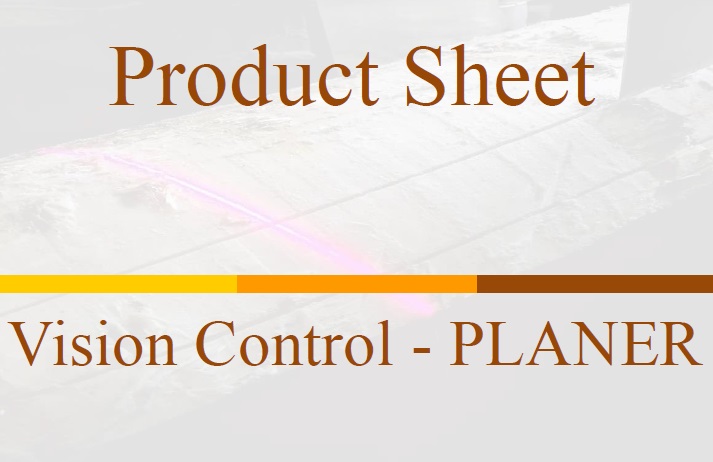
Vision Control - SAW
Vision Control – SAW – Is a control system for non-contact thickness measurement of the products produced in a saw line.
Vision Control – SAW – Is the market leader and can be selected to be installed in a primary or a secondary saw group, or in your resaw equipment
Vision Control – SAW Is able to measure on sawn pieces with vane and present a very high measurement accuracy 0,2 mm or better.
HMI – The operator interface is user-friendly and presented on a monitor screen.
Function of Correction – As an option, the Auto Correction extension can be selected. The measurement system measures and performs calculations and analyses of up to 4000 metrics per sawn piece and based on average calculations, the system sends a correction to the parent PLC system and the machine equipment corrects to the desired set raw sizes.
Semi correction: The operator receives a correction proposal and approves alt rejects.
Auto correction: Corrections are performed automatically
Reports – The system automatically creates a report after each completed posting and all metrics are saved in a database, in order to be analyzed later
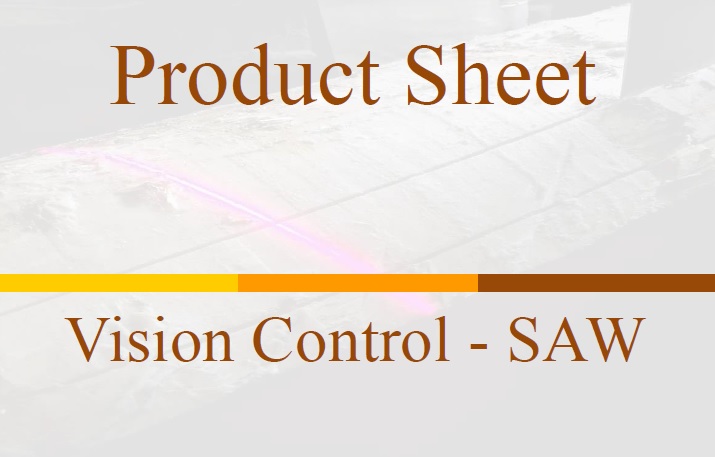